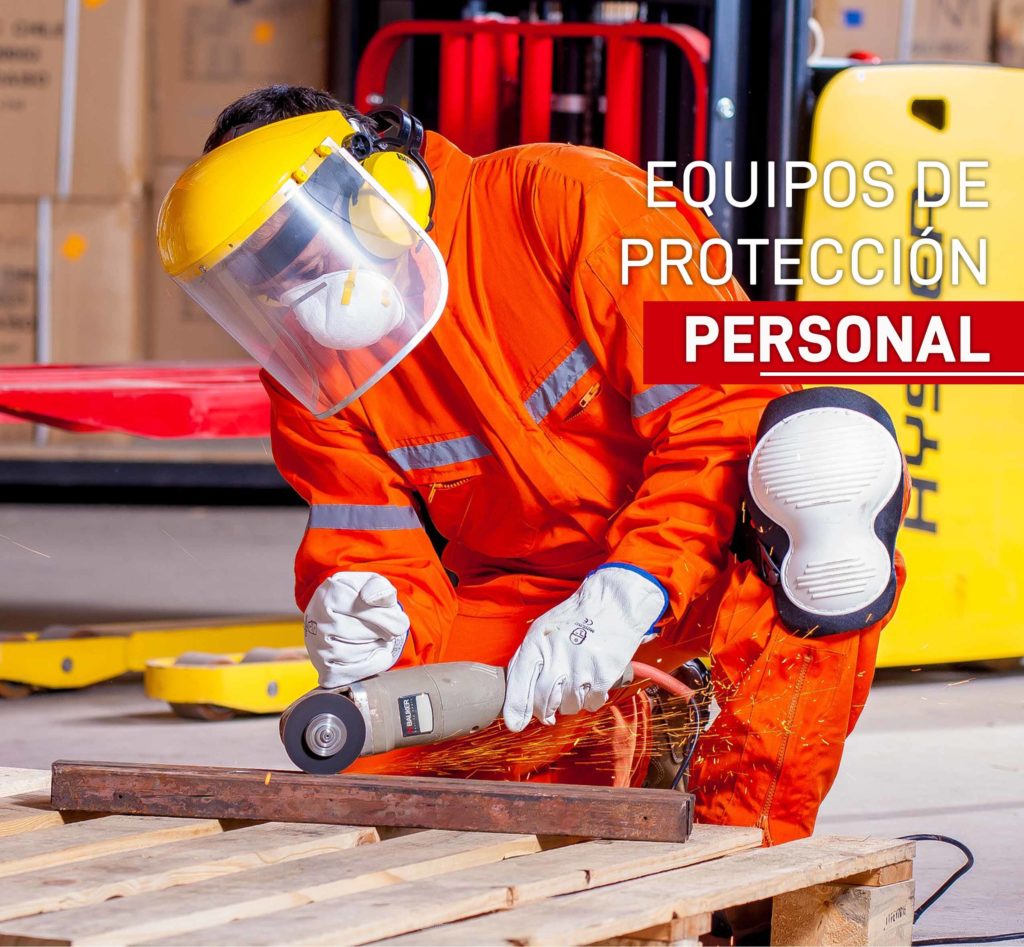
The Occupational Safety and Health Administration (OSHA) explains that personal protective equipment, commonly known as “PPE,” are devices used to minimize exposure to hazards that cause serious injury and illness in the workplace. These injuries and illnesses can result from contact with chemical, radiological, physical, electrical, mechanical, or other hazards in the workplace.
HOW DO I KNOW IF I NEED TO USE PERSONAL PROTECTIVE EQUIPMENT?
Generally, the governmental entities of each country require employers to carry out a risk assessment in the workplace, to identify area associated risks and assess whether there is a need for workers to use protective equipment. The objective of this study is to identify the risk, analyze whether it can be eliminated or minimized, actions to be followed and compliance with the pertinent regulations.
OSHA indicates that the use of personal protective equipment is usually essential, but it is the last alternative after the engineering controls, work practices and administrative controls are carried out, in order to eliminate or minimize the risks associated with the work area.
- Engineering controls relate to the physical modification of a machine or the work environment.
- Administrative controls involve modifying how and when workers perform their tasks, such as: work hours and worker rotation to reduce exposure to risks.
- Work practices involve training workers in how to perform tasks that reduce exposure hazards in the workplace.
When engineering, labor practice and administrative controls are not feasible or do not provide sufficient protection, employers must provide personal protective equipment to their workers and ensure its proper use.
HOW TO ENSURE THE PROPER USE OF PERSONAL PROTECTIVE EQUIPMENT?
OSHA explains that workers must be trained in the correct use of personal protective equipment, reporting the following:
- Properly use personal protective equipment.
- Know when personal protective equipment is necessary.
- Know what type of personal protective equipment is necessary.
- Know the limitations of personal protective equipment to protect employees from injury.
- Putting on, adjusting, using, and removing personal protective equipment.
- Keep personal protective equipment in good condition. Proper equipment care, maintenance, life, and disposal.
If PPE is to be used, a PPE program must be implemented. This program must address the dangers present; the selection, maintenance and use of PPE; employee training; and monitoring the program to ensure its continued effectiveness.
TYPES OF PERSONAL PROTECTIVE EQUIPMENT
Personal protective equipment allows to protect those parts of the worker’s body that are exposed to risks. Here is its classification according to OSHA:
HEAD PROTECTION
Safety helmets can protect workers from impacts to the skull, deep injuries, and electrical shock such as those caused by falling or floating objects, fixed objects, or contact with electrical conductors.
For more information visit the HEAD PROTECTION section.
HEARING PROTECTION
Exposure to high levels of noise can cause irreversible hearing loss or disability, as well as physical or psychological stress. Short-term exposure to loud noises can also cause a temporary change in hearing, symptoms may disappear within a few minutes to hours after leaving the noise. However, repeated exposure to loud noise can lead to permanent damage or loss of hearing. Exposure to noise in the workplace over many years can lead to irreversible hearing loss if daily acoustic exposure levels reach or exceed 85 dB.
Earplugs or earmuffs can help protect your ears from noise exposures. For more information visit the HEARING PROTECTION section.
EYE AND FACE PROTECTION
Workers in certain work areas are at risk of being impacted on the face and eyes by material fragments, large chips, hot sparks, optical radiation, molten metal splashes, as well as particles, sand, dirt, vapors, dust, and glows.
Safety glasses, screens, and googles can help protect the face and eyes from external agents. For more information visit the EYE AND FACE PROTECTION section.
HAND PROTECTION
Workers exposed to harmful substances through skin absorption, deep cuts or lacerations, serious abrasions, chemical burns, thermal burns, and harmful extremes of temperature should protect their hands by wearing safety gloves, mittens, and thimbles.
For more information visit the section on HAND AND ARM PROTECTION.
BODY PROTECTION
In certain cases, workers must protect their body from workplace hazards, such as exposure to heat and radiation, hot metals, boiling liquids, organic liquids, dangerous materials, among others.
There are aprons, sleeves, and protective clothing made of fire-retardant cotton and wool materials, rubber, leather, synthetics, and plastic that help protect the body.
For more information visit the INDUSTRIAL CLOTHING section.
RESPIRATORY PROTECTION
Before the possibility of inhaling chemical products, mists, gas fumes, we must protect the respiratory tract. Respiratory equipment generally covers the nose and mouth, or the entire face or head, and helps prevent injury or illness. The main respiratory protective equipment are masks, cartridge respirators, special filters, and self-contained air.
For more information visit the RESPIRATORY PROTECTION section.
FOOT PROTECTION
Foot injuries or accidents are often caused by not wearing proper protection and can be avoided by wearing safety footwear appropriate for the hazard or area involved.
Safety shoes protect workers from the risks associated with their feet, such as: falls on level, slides, entrapment, electric shock, among others. For more information visit the FOOT PROTECTION section.
Source: The Occupational Safety and Health Administration (OSHA).
COMPARTIR / SHARE: